Heidelberg Materials supplies concrete for the construction of the largest wind farm in the Baltics
Innovative digital solution enabled the use of carbon reduced cement in the concrete mix.
Sopi-Tootsi solar and wind farm, located on a depleted peat deposit in North Pärnu County, Estonia is currently under construction. By the end of 2024 a total of 38 wind turbines will be operational in the area. Heidelberg Materials is supplying more than 100 truckloads of concrete for the foundations every casting day.
The customer is an Estonian construction company NOBE who is providing building contracting services and concrete work for Enefit Green, Estonia's largest wind farm developer. Upon completion Sopi-Tootsi will be the largest renewable energy area, not only in Estonia, but across the Baltics in terms of capacity providing more than 680 gigawatt-hours of renewable electricity per year.
Delivery and quality assurance is essential
"As the concrete for the wind turbine foundations requires a large quantity of high quality concrete in a short period of time - the concrete casting has to be done at a very fast pace and without breaks - we were looking for a supplier with a sufficiently large network of plants and machinery. This was to ensure that if, for example, a technical failure occurred with a concrete plant or pump, the supplier would be able to quickly resume deliveries and replace the pumps. Heidelberg Materials was able to provide us with this supply and quality assurance” says Andrei Gerasimenko, Head of the Concrete Works at NOBE.
According to Indrek Rahu, General Manager of Heidelberg Materials Betoon, the concrete needed for the foundations of one wind turbine is delivered simultaneously from two or three of the company's plants within 10 to 14 hours. That's how long it takes to cast a single foundation, and more than 100 concrete trucks are loaded every casting day. "If you line up these trucks one after the other, you get a line of trucks a kilometre long," explains Rahu.
The wether has been a challenge
As the whole project will take eight months - it started in the summer of 2023 - the weather and different seasons have been a challenge for the contractor. The concrete casting had to be carried out both in the summer heat, when the thermometer read over 25 degrees, and in the winter, when it was 15 degrees in January. "Our concrete plant crews, as well as the workers on site casting the concrete mix, had to adapt to all of this. Winter conditions in particular have been challenging - low temperatures, snow, slippery roads and dark weather. Our team managed well," says Rahu.
Innovative digital solution saved resources and nature
When casting such complex and massive structures, the builder's requirements specify a maximum curing temperature for the concrete of the foundation structure - too high a temperature during curing could damage the properties of the concrete. To monitor the temperature of the concrete mix, innovative Giatech SmartRock sensors offered much support to the contractor. ”Installing them in the structure was easy. The graph generated from the temperature data collected by the sensors could be monitored by the site team in real time on the screen of a smart device. All this saved time," says Andrei Gerasimenko.
Secondly, the information gathered by the SmartRock sensors also allowed decisions to be made on the choice of cement, resulting in reduced carbon emissions from the casted concrete.
"For the concrete mix, we supplied a total of three types of cement from Kunda plant. As a result of continuous temperature monitoring, we were able to switch from the low-heat loss CEM I type cement to carbon reduced and more cost-effective CEM II cements - Composite Cement and Construction Cement - as soon as temperatures allowed. Thereby we were able to reduce carbon footprint of one foundation by about 130 tonnes," says Rahu.
Construction of the wind farm has now reached the stage where casting of foundations is almost completed, and erection of the wind turbines will start in March. The wind farm will be put into operation in September 2024.
-
Facts
- • At the start the wind turbines will be generating around 680 gigawatt-hours of renewable electricity per year, doubling Estonia's total wind energy production. This will amount to nearly 8.5% of the total electricity consumed in Estonia and 40% of the electricity demand of domestic consumers, covering the electricity consumption of around 200 000 households in Estonia at the same time saving 700,000 tonnes of CO2 from being emitted into the atmosphere.
- • Wind energy has become one of the most important sources of renewable energy, helping to reduce the environmental impact of fossil fuel use. In Estonia, the need for such renewable energy buildings has been growing over time. Large-scale facilities such as wind farms require versatile construction solutions, of which concrete is an important component. Concrete's strength and durability make it a suitable material for wind turbine foundations, ensuring the wind turbines' resistance and stability to storms and weather conditions.
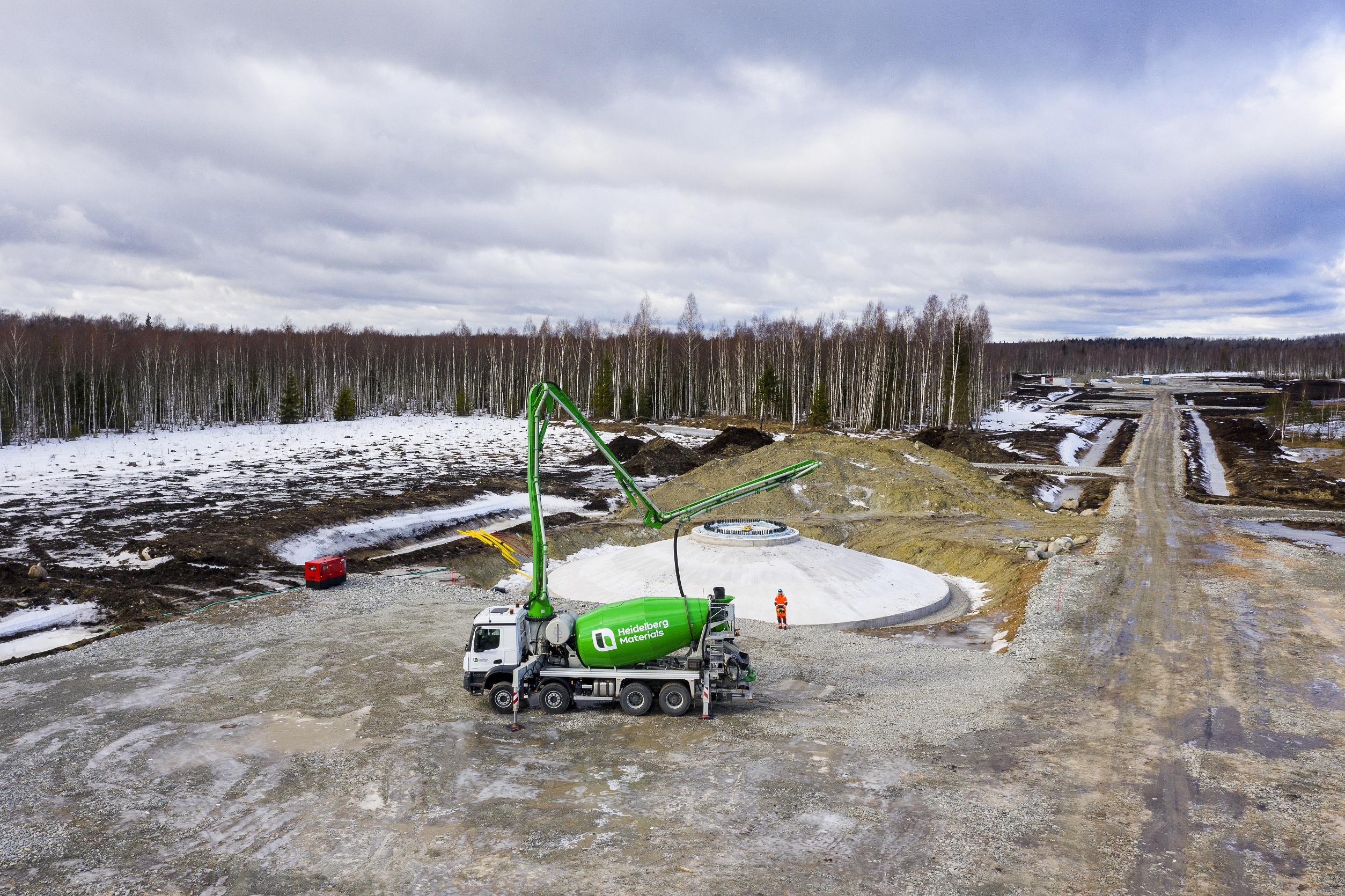
The construction site of Enefit Green`s Sopi Tootsi wind farm (4).
The construction site of Enefit Green`s Sopi Tootsi wind farm (3). Two concrete pumps were used to cast each foundation.
The construction site of Enefit Green`s Sopi Tootsi wind farm (2). Two concrete pumps were used to cast each foundation.
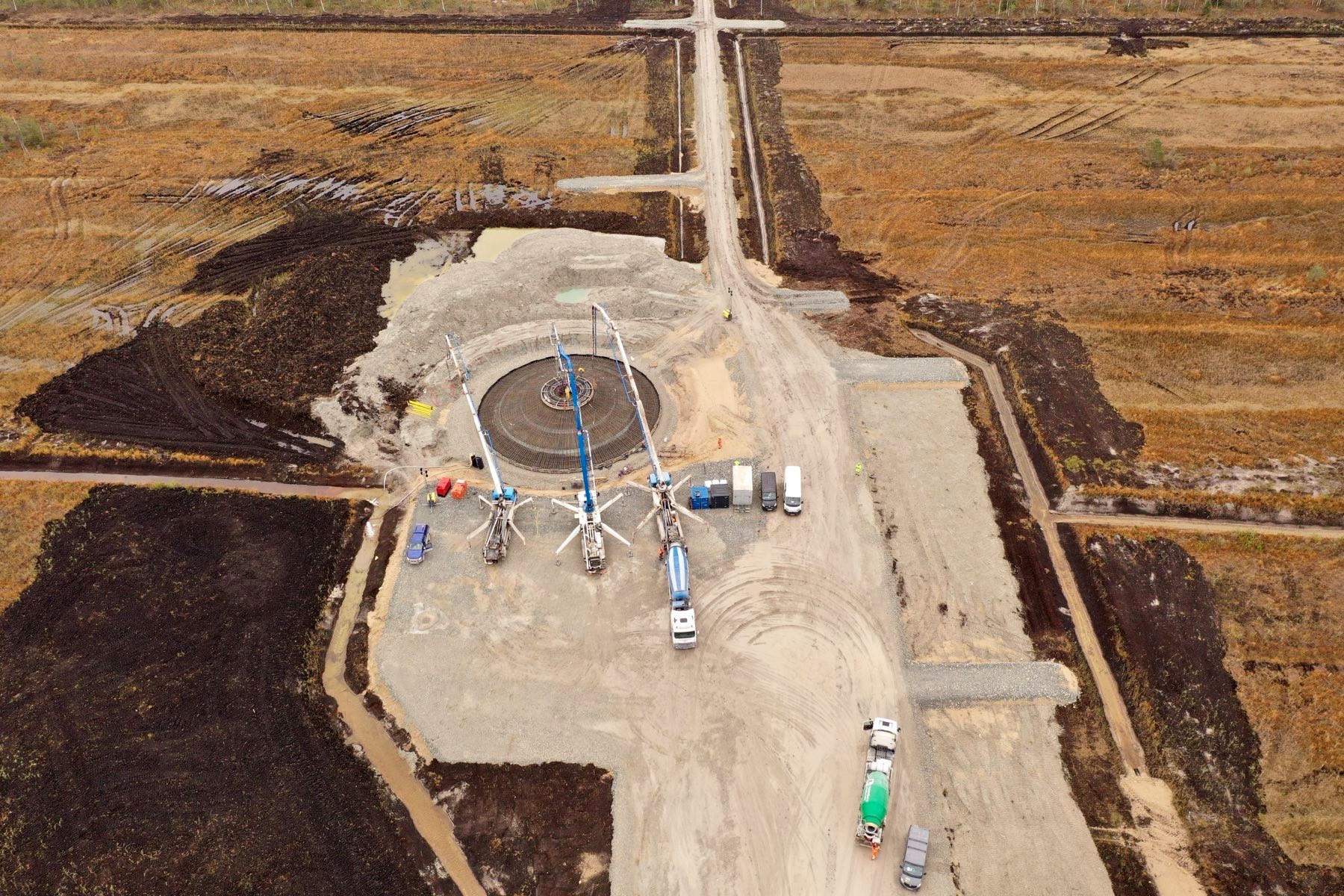
The construction site of Enefit Green`s Sopi Tootsi wind farm (1).
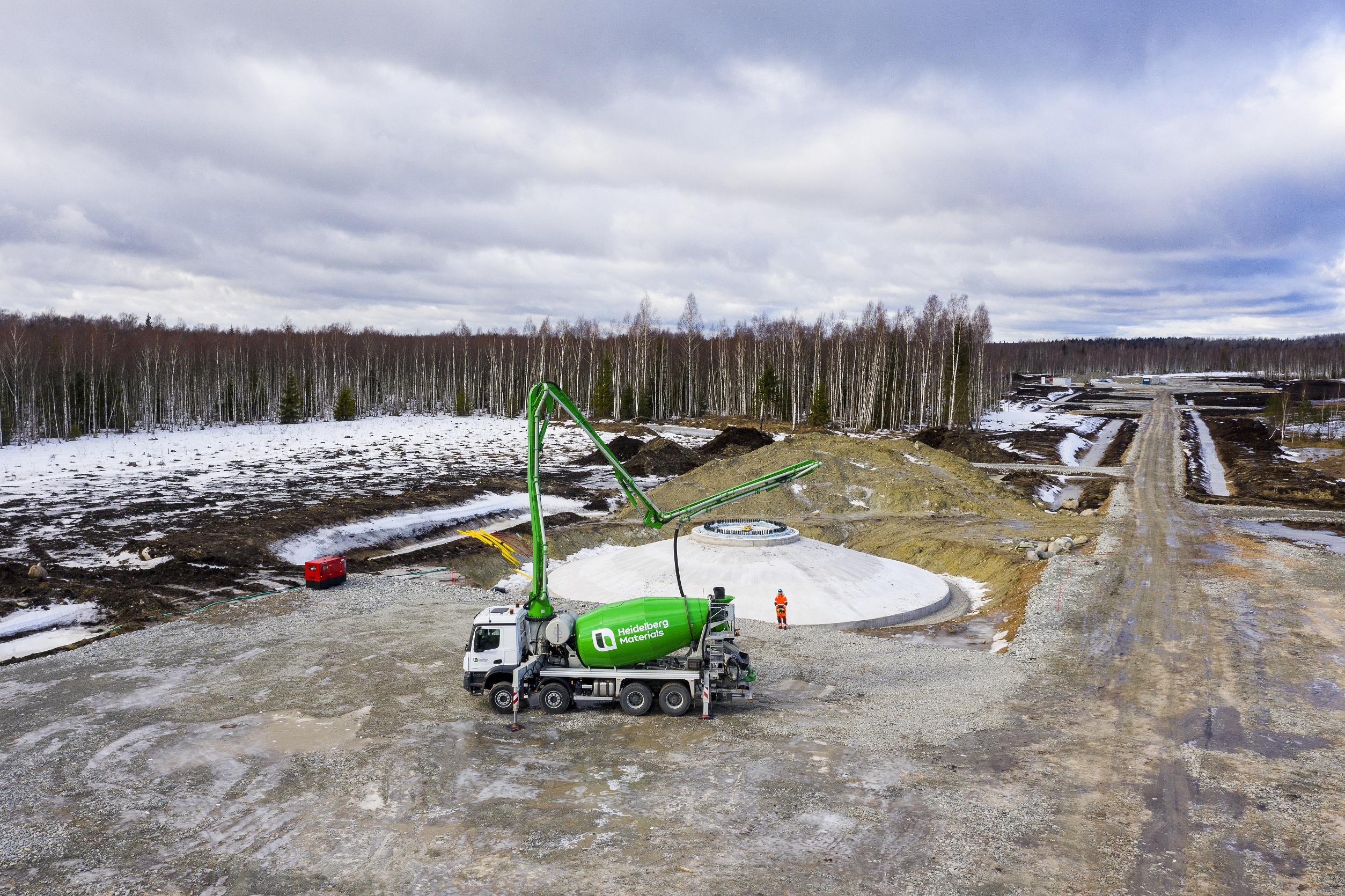
The construction site of Enefit Green`s Sopi Tootsi wind farm (4).
The construction site of Enefit Green`s Sopi Tootsi wind farm (3). Two concrete pumps were used to cast each foundation.
The construction site of Enefit Green`s Sopi Tootsi wind farm (2). Two concrete pumps were used to cast each foundation.
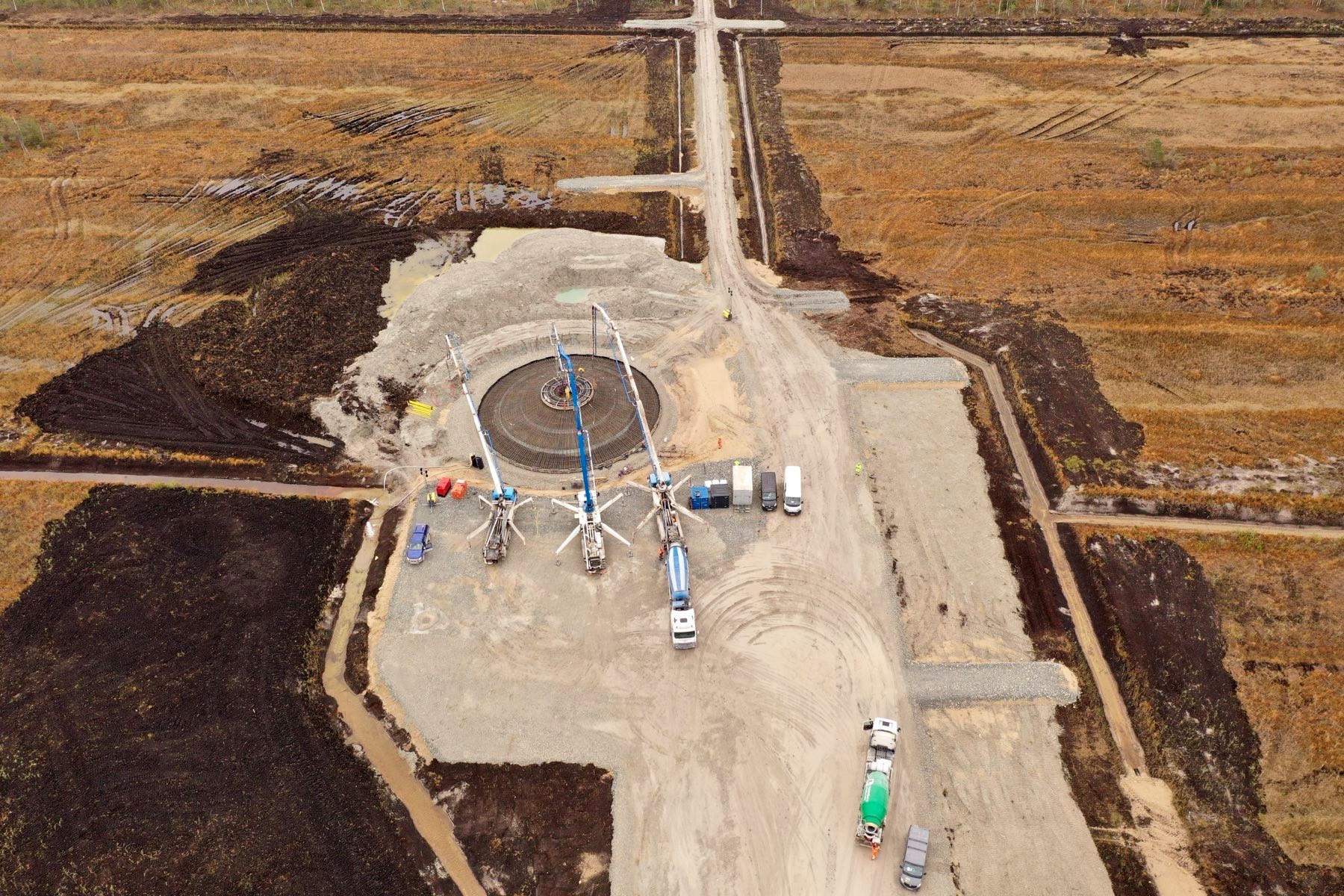
The construction site of Enefit Green`s Sopi Tootsi wind farm (1).