Inauguration of Europe's most modern sleeper plant
Yesterday, Heidelberg Materials celebrated a milestone with the inauguration of the new sleeper production facility in Vislanda, Sweden. The investment of around 4 million euro enables efficient, high-quality and precision-safe production of railway sleepers.
"In 2.5 years, we have gone from sketch to completion. Now we look forward to continuing to deliver Europe's best sleepers with the most modern technology to a growing market", said Managing Director Filip Sten.
Employees, customers, suppliers, partners and representatives of the municipality of Alvesta attended the event at the plant, where Filip Sten and Plant Manager Lisa Conradsson Hult gave speeches and cut the ribbon. This was followed by a tour and demonstration of the plant.
Advanced production equipment
The new production equipment includes seven 110-metre-long casting beds, a cutter, robotic assembly and handling, and an automated unloading conveyor. This ensures a capacity of 1200 sleepers per day. To build one kilometre of railway, 1666 sleepers are needed, and each sleeper weighs around 300 kilograms.
Heidelberg Materials, formerly known as Abetong, has been producing sleepers at the Vislanda plant since the 1950s. Today, Heidelberg Materials is one of two suppliers of sleepers in Sweden, with the Swedish Transport Administration as its main customer.
Budget and schedule have been kept
The previous production equipment was in urgent need of upgrading. Just over two years ago, the idea of a modernised plant became concrete. After the investment was approved in 2023, planning and preparation followed. In the summer of 2024, construction work started with demolition, new construction and installation.
Lisa Conradsson Hult, plant manager for the past ten months, says:
"I came in when the project was already in full swing. It's been a very pleasant journey and I'm proud to be part of our exciting future. The commitment of the employees and the project managers has been tremendous!"
More sustainable production
In addition to more efficient production equipment, the Vislanda plant has gradually reduced the carbon footprint of its production, partly to meet the requirements of the Swedish Transport Administration.
Recipe optimisation, pellets for heating, recycled crushed concrete instead of virgin aggregate in the new concrete, LED lighting in the plants and transport that runs on environmental fuel are some examples of environmental improvement measures that have been taken. Overall, it has reduced the climate impact by 20% in five years.
"Now we are ready for the next step in sustainable concrete construction. With our new evoZero cement, we will be able to reduce the climate impact of a sander by a further 60% in one go," says Filip Sten.
Downloads
Inauguration of sleeper’s plant Vislanda.
Inauguration of sleeper’s plant Vislanda.
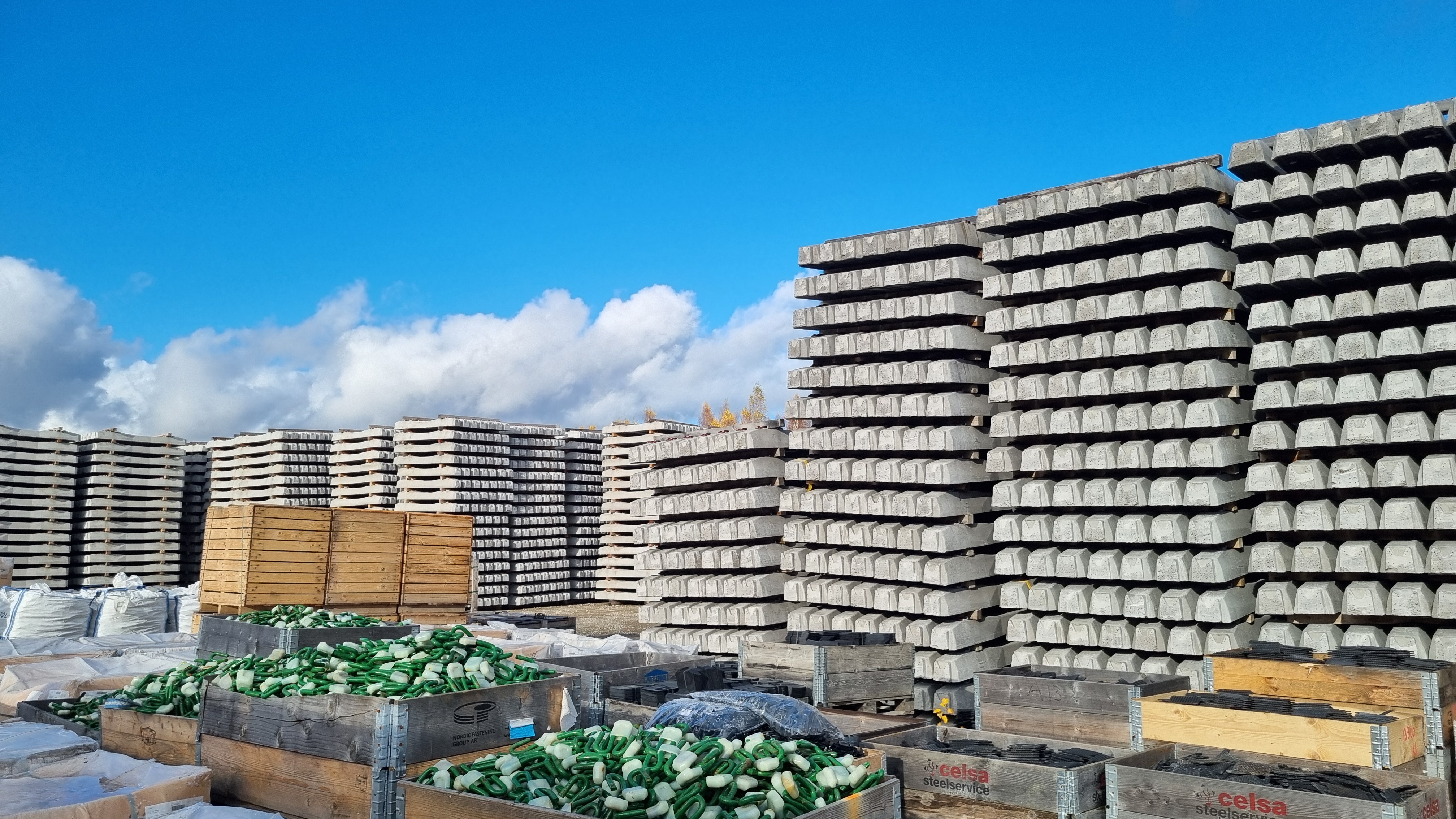
Inauguration of sleeper’s plant Vislanda - concrete sleepers.
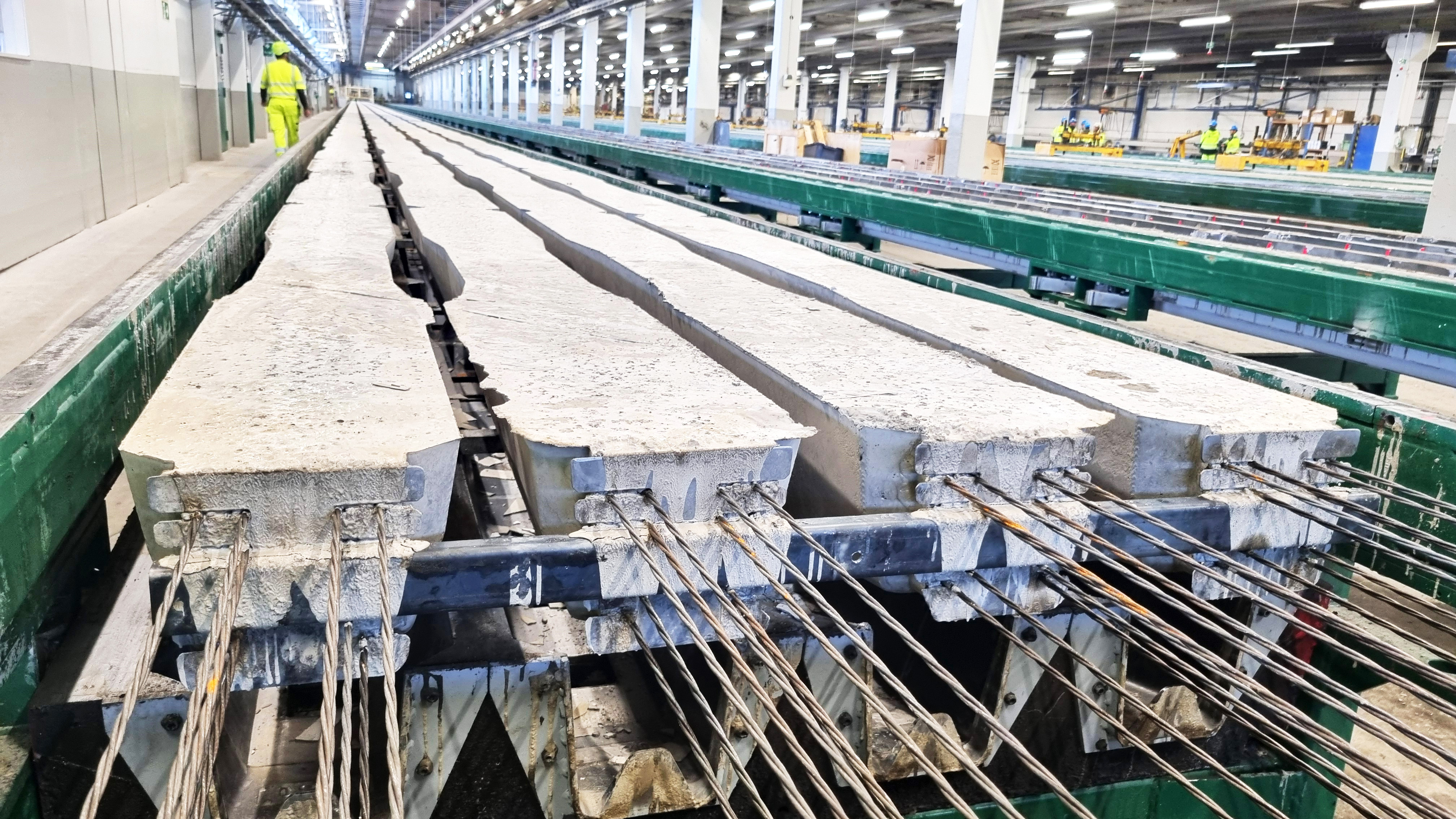
Inauguration of sleeper’s plant Vislanda.
Inauguration of sleeper’s plant Vislanda.
Lisa Conradsson Hult, plant manager.
Inauguration of sleeper’s plant Vislanda.
Inauguration of sleeper’s plant Vislanda.
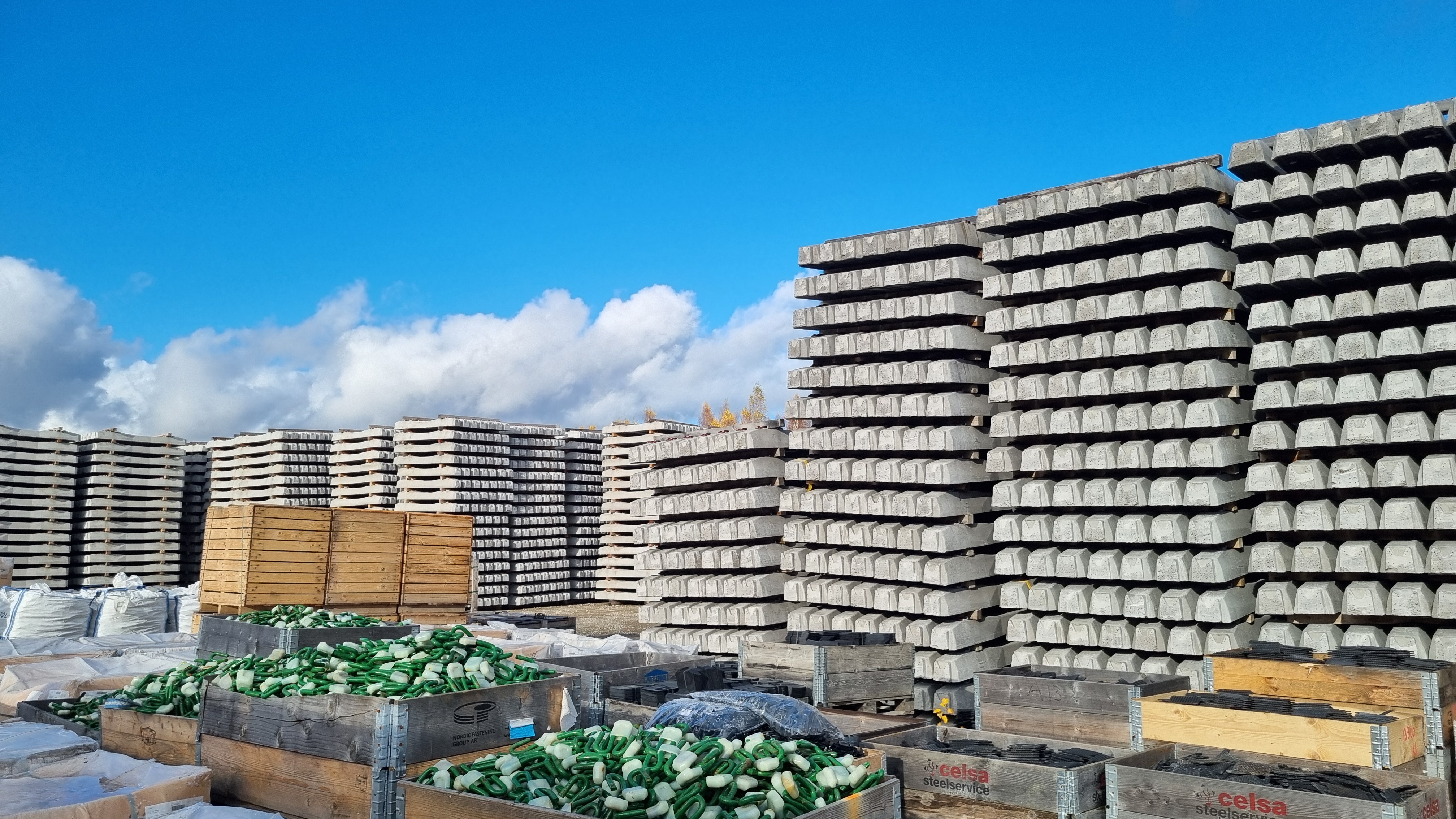
Inauguration of sleeper’s plant Vislanda - concrete sleepers.
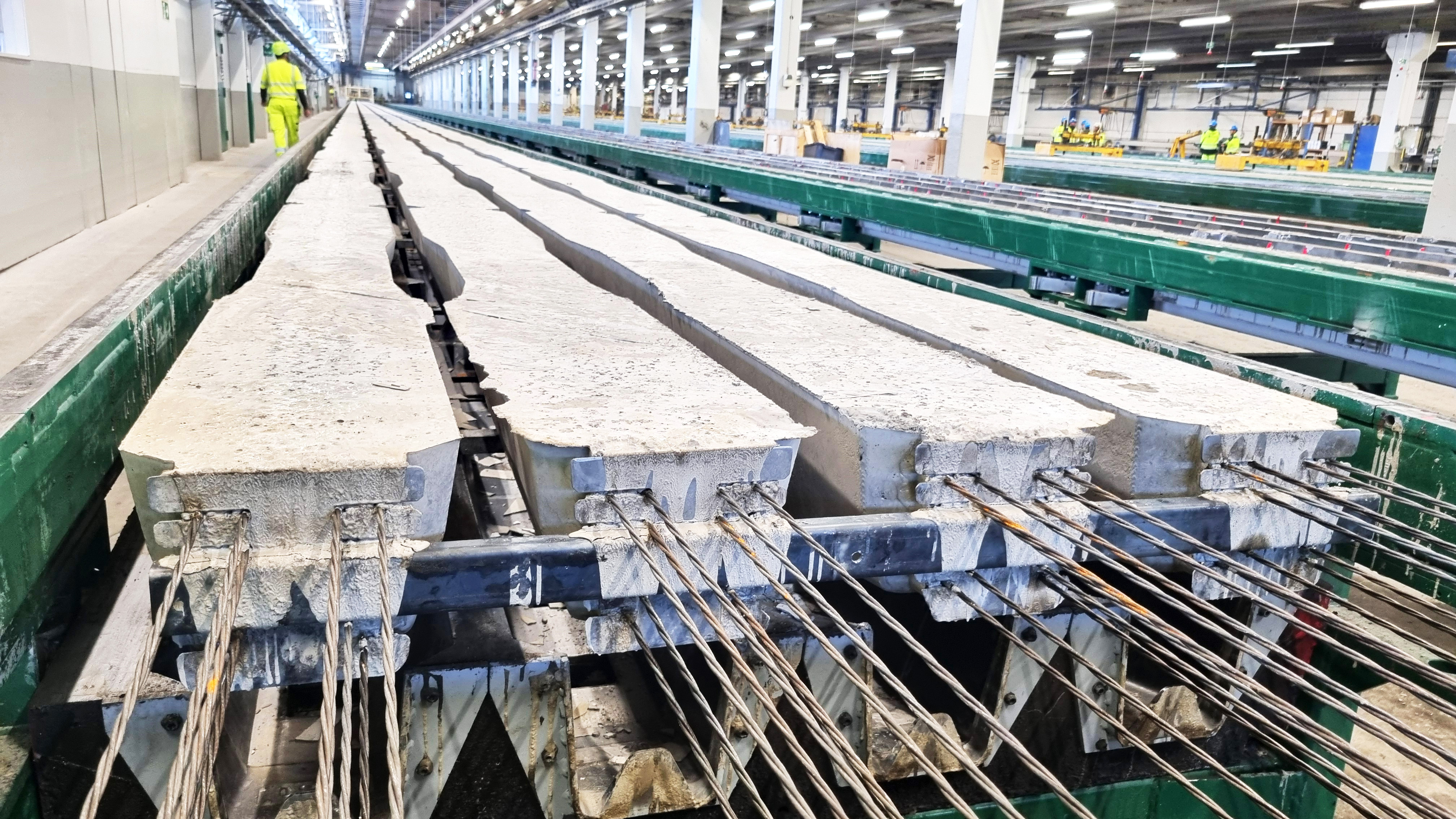
Inauguration of sleeper’s plant Vislanda.
Inauguration of sleeper’s plant Vislanda.
Lisa Conradsson Hult, plant manager.